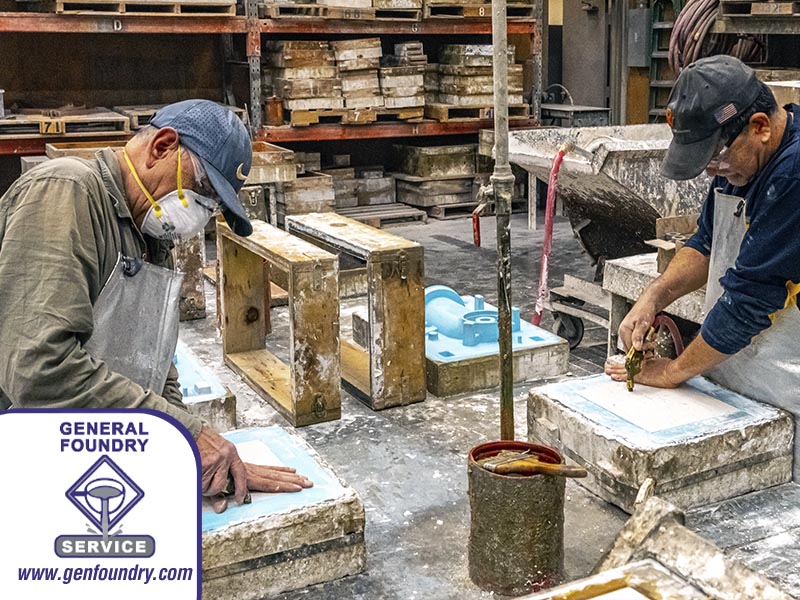
For engineers developing metal components, selecting the proper casting process and the right foundry partner is fundamental to product success. It determines not only part geometry parameters, tolerances, and material performance, but also impacts downstream processes, total cost, and time to market.
At General Foundry Service, we specialize in five distinct casting processes under one roof, each tailored to a different segment of the design-performance-cost envelope. Here, we provide a brief technical framework for evaluating casting options using each method’s specific capabilities and advantages to guide process selection.
1.) Understand Functional Requirements Before Selecting the Process
Each casting method has inherent process capabilities and limitations. The key to successful casting design begins with a firm understanding of:
- Geometric complexity: Undercuts, hollow features, and nominal wall section
- Mechanical properties: Static strength, fatigue resistance, impact behavior
- Surface finish and as-cast tolerances
- Production volume and repeatability needs
- Tooling cost vs. part cost trade-offs
- Post-processing and finishing operation requirements
Let’s compare the five casting processes General Foundry offers from a technical standpoint:
2.) Casting Process Comparison
Green Sand Casting
- Process Summary: Economical and quick, uses moist sand and clay packed against a pattern
- Best for: Simple to complex geometries, small to large parts (~100 lbs)
- Tolerances: ±0.030 in (depending on size and parting line complexity)
- Surface Finish: 125 RMS
- Pros:
- Low tooling and piece price cost
- Easy and low cost to modify tooling
- Excellent for prototyping or low- to medium-volume
- Fast mold cycle times and short lead times
- Cons:
- Larger dimensional accuracy compared to other processes
No-Bake (Air Set) Sand Casting
- Process Summary: Chemically bonded sand, cured at ambient temperature, packed against a pattern
- Best for: Large parts (100-500 lbs) and simple to complex geometries
- Tolerances: ±0.030 in (depending on size and parting line complexity)
- Surface Finish: 125-200 RMS
- Pros:
- Good dimensional stability
- Accommodates complex geometry
- Ideal for larger parts not suited to green sand or investment
- Lower cost tooling for size of parts
- Easy to modify tooling
- Cons:
- Slower and costs more than green sand
Permanent Mold Casting
- Process Summary: Uses negative metal molds (usually H-13 steel or iron), often with gravity pouring
- Best for: High-volume production of relatively simple parts with high consistency
- Tolerances: ±0.020–0.30 in/in
- Surface Finish: 125-200 RMS
- Pros:
- Excellent repeatability and surface finish
- Better mechanical properties due to faster cooling rates (finer microstructure)
- Shorter cycle times over time leading to lower per piece price
- Cons:
- Higher initial tooling cost
- Expensive to modify tooling
- Limited to smaller overall part size (~50 lbs)
Rubber Plaster Mold (RPM) Casting
- Process Summary: A silicone rubber positive tool is created from a printed or machined master negative pattern; plaster slurry is poured against the rubber tool to create molds
- Best for: Thin-walled (2 mm-4 mm), smaller geometries (<50 lbs), low volume production, prototype, and bridge die production
- Tolerances: ±0.010–0.030 in/in
- Surface Finish: 63 RMS
- Pros:
- Thin wall casting (as low as 0.0640″)
- Excellent detail and precision
- Low-cost tooling and tooling iterations
- Minimal to no draft required
- Cons:
- Lower mechanical properties due to longer freeze time
- Not suited for high production volumes
Investment (Lost Wax) Casting
- Process Summary: Wax patterns are assembled into trees, a solid mold is created, then dewaxed before pouring
- Best for: Intricate parts with tight tolerances, no draft, and complex internal features
- Tolerances: ±0.005–0.010 in/in
- Surface Finish: 63 RMS (or better)
- Pros:
- Excellent dimensional precision
- Allows complex geometries and thin walls
- Minimal to no draft needed
- Cons:
- Higher tooling and per-part costs
- Limited to smaller-sized parts (due to costs)
3.) Material Behavior and Casting Suitability
Different alloys exhibit varying castability, solidification shrinkage, and reaction to mold materials. General Foundry’s metallurgists assist in selecting the right alloy for:
- Thermal performance
- Corrosion resistance
- Weldability and post-processing
- Mechanical strength
For example: A356-T6 aluminum offers a high strength-to-weight ratio, while ALMag 535 offers increased elongation but is less castable.
4.) Designing for the Casting Process (DFM)
Collaborating early in the design cycle ensures manufacturability. At General Foundry, we can provide:
- Solidification modeling
- Corebox and gating design optimization
- Advice on draft, wall thickness, radii, and transitions
- Tolerance stacking for multi-cavity or large-part applications
Each casting method has DFM considerations. For example, investment casting can support zero-draft features, while permanent mold casting demands larger draft angles (typically >3°) to facilitate part ejection.
5.) Post-Casting Operations and Integration
High-performance parts often require secondary operations, which we can perform in-house for quality and time control:
- CNC machining to medical and aerospace tolerances
- Anodizing, chromating, and powder coating
- Non-destructive testing (FPI, X-ray, ultrasonic)
- Heat treating for property optimization (T6, T7, etc.)
This integrated approach reduces delays and variation, ensuring the final component matches the specification without quality concerns.
With five casting processes, in-house machining, and an experienced engineering team (over 100 years combined), General Foundry Service enables engineers to optimize for performance, manufacturability, and cost without compromise. Our process-agnostic approach means we match your requirements to the best solution, not vice versa.
How can General Foundry Service help you?
With nearly 80 years of casting experience in various critical industries, General Foundry provides you with “get it right the first time” quality and a customer-focused approach to each project. We offer best-in-class turnkey solutions with multiple processes and alloy options to meet your component needs. Contact us today for more information or to get started on your next project.