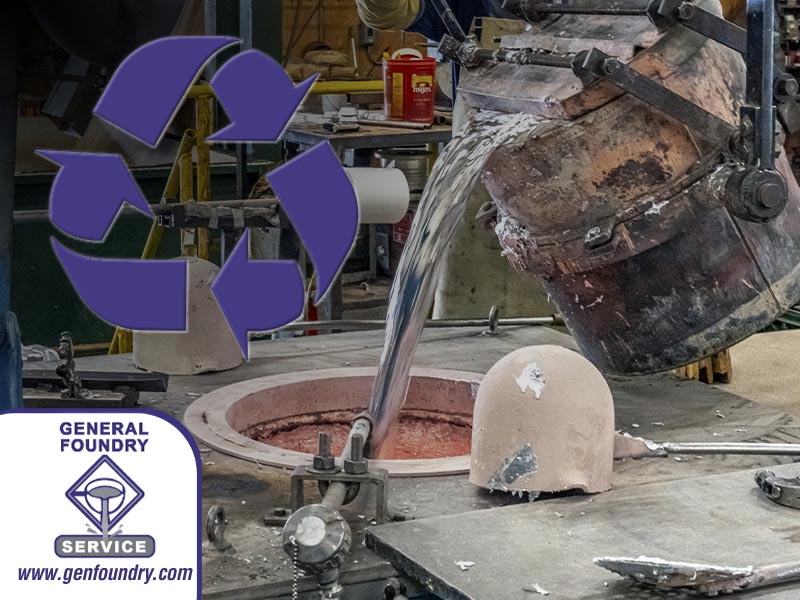
Sustainability is emerging as a key focus in almost every industry, and metal parts or device manufacturing is no exception. This shift is driven by a growing awareness of environmental impacts and a responsibility towards eco-friendly practices. Manufacturers are constantly looking at ways to:
- Reduce their carbon footprint
- Conserve resources
- Utilize recyclable materials
- And more
Creating sustainable metal parts and devices presents unique challenges. It requires balancing environmental considerations with the desired quality and safety standards. Innovations in this area include (but are not limited to):
- Using biodegradable or recyclable materials
- Improving energy efficiency in production
- Minimizing waste through lean manufacturing processes
Are sand cast parts sustainable?
Sand cast parts contribute to recyclability and sustainability efforts by promoting the reuse of materials and utilizing energy-efficient practices. The sand used in casting can be reclaimed and reused multiple times with minimal processing, reducing waste and lowering the environmental impact. The metals involved, such as aluminum, iron, and steel, are also highly recyclable, meaning scrap metal from cast parts can be melted down and repurposed without degrading the material quality. This circular use of materials reduces the need for new raw resources and limits energy consumption in mining and refining. Additionally, sand casting processes are adaptable to small and large production runs, reducing overproduction and further minimizing waste.
However, the sustainability of sand casting depends on adequately managing resources, such as controlling emissions from furnaces and minimizing waste during the molding and casting processes. Technological advances, such as improved sand reclamation and energy-efficient furnaces, are helping to make sand casting more eco-friendly.
What about Rubber Plaster Mold (RPM) casting?
RPM casting creates highly accurate parts with fine details, which helps decrease material waste during the machining or finishing stages. Using reusable rubber molds further enhances sustainability, as these molds can be repurposed multiple times before needing replacement. Additionally, metals used in RPM casting, like aluminum and magnesium, are highly recyclable, allowing for the recovery and reuse of scrap material without compromising quality.
However, the plaster used in the process is typically single-use and less recyclable compared to sand. Advances in more eco-friendly plaster formulations and improved recycling techniques could further enhance the sustainability of RPM casting. The process’s ability to produce precise parts with minimal excess material reduces energy consumption and waste in critical part manufacturing.
Sustainable and environmentally friendly manufacturing
As sustainability continues to gain momentum, it will continue to shape future innovations in cast metal device manufacturing. This shift towards eco-friendly practices benefits the environment and can lead to cost savings and improved public perception for manufacturers. For engineers and designers, this means adapting to new materials, processes, and methods. It involves rethinking designs to incorporate sustainability from the ground up, selecting materials with lower environmental impact, and designing for easier disassembly and recycling.
How can General Foundry Service help you?
With nearly 80 years of casting experience in various critical industries, General Foundry provides you with “get it right the first time” quality and a genuinely customer-focused approach to each project. We offer best-in-class turnkey solutions with multiple processes and alloy options to meet your component casting needs. Contact us today for more information or to get started on your next project.