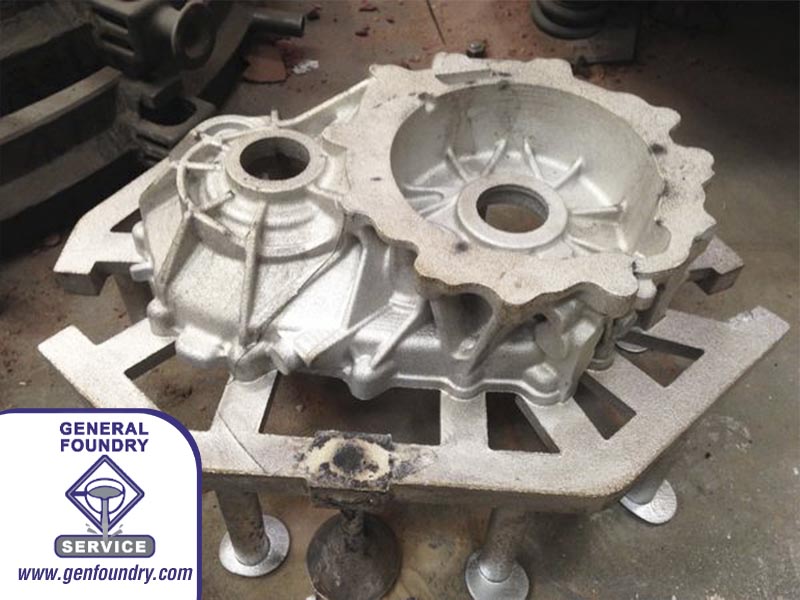
3D printed sand mold castings, or additive manufacturing sand casting, are a modern approach to traditional sand casting using 3D printing technology. This method combines the benefits of both additive manufacturing and traditional casting techniques to create simple or very complex cast metal components.
The 3D Printed Sand Mold Casting manufacturing process
The 3D printed sand mold casting process typically consists of:
- Design and 3D Printing the Sand Mold: The process begins with a customer sending their unique geometry to be cast. General Foundry then CADs up the mold with down sprues, gating, and risers. The model of the gating is then usually simulated to ensure proper fill and flow. Once gating is confirmed, the mold package dimensions are minimized to optimize for space and cost on the 3D sand printer. Using a 3D sand printer the gating and mold cavity is produced layer by layer. This involves depositing thin layers of sand and binder material, often using a process called binder jetting. The binder is selectively jetted onto the sand particles to bind them together and form the desired shape of the mold.
- Mold Assembly: Once the 3D printed sand mold is complete, it may consist of multiple parts that must be assembled to create the mold cavity. This can involve aligning and securing the different mold sections.
- Casting: The mold is prepared for the casting process, which involves removing any loose or excess sand particles. The mold is then filled with molten metal, as it would be in traditional sand casting. The metal is poured through a gating system that directs the flow and helps prevent defects.
- Cooling and Solidification: The molten metal cools and solidifies within the 3D printed sand mold, taking on the shape of the mold cavity. The cooling and solidification time varies based on the size of the casting and the metal used.
- Mold Removal and Finishing: Once the metal has solidified, the 3D printed sand mold is broken away or removed to reveal the cast metal part. This step is also similar to the mold removal process in traditional sand casting, as each mold is a one-time use mold. The casting will likely undergo additional finishing processes such as grinding, machining, powder coating, or liquid painting to achieve the desired final specifications and surface finish.
Why select this process for your parts?
This accurate, timely, and cost effective prototype casting process utilizes 3D printing technology and eliminates the need for intricate core boxes or traditional tooling. 3D printed sand mold can provide significant advantages over standard prototype casting methods; including reduced lead time, less labor associated with pattern/tooling creation, and the ultimate design freedom.
Some of the advantages of selecting 3D printed sand molds include (but are not limited to):
- Complex Geometries: 3D printing enables the creation of intricate and complex mold geometries that might be difficult or impossible to achieve with traditional sand casting techniques, like zero draft geometries.
- Design Flexibility: Changes to the design can be easily incorporated into the 3D CAD model, and the updated mold can be printed relatively economically and quickly.
- Rapid Prototyping: This method allows for the rapid production of molds, reducing the lead time for producing prototypes or small batches of castings.
- Reduced Tooling Costs: Traditional casting methods require tools and patterns. 3D printing eliminates or reduces the need for these traditional tooling components.
- Printed Sand Cores: Complex and fragile sand core assembles may be printed as one piece, reducing tooling costs, labor and scrap.
How can General Foundry Service help you?
General Foundry offers 3D printed sand mold castings for your accurate, economical, and timely prototype casting needs. The 3D printer is like any inkjet printer, except instead of printing ink, the machine builds layers of sand to create a one-time use sand (negative) molds. There are opportunities to combine cores and integrate this technology in production, but it is geometry specific.
General Foundry Service offers true one-stop shopping. With our in-house pattern shop, machine shop, and five complementary casting processes, we specialize in machined, Class A cosmetically coated aluminum castings. Contact us today for more information about our clean metal casting solutions or to get started on your next project.