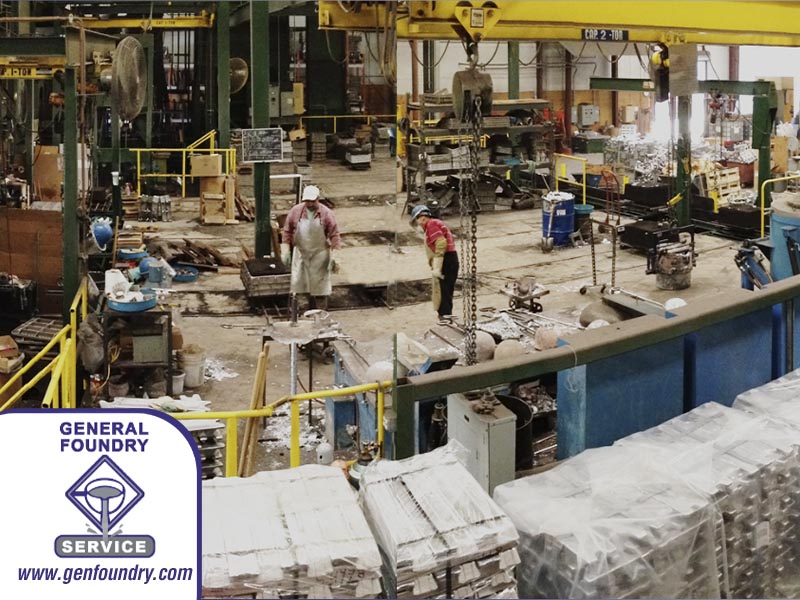
The metal casting industry is the backbone of the U.S. manufacturing economy due to its role in supporting various critical sectors of the economy, technological innovation, national defense, and more. It is a $46 billion industry that employs nearly 490,000 people.
There are many different types of casting processes available. Each has its advantages and drawbacks. Understanding these distinctions can be essential to creating quality components for your industry.
This article briefly overviews six (6) metal casting processes. Please keep reading to learn more about their differences to help you decide which would work best for your next metal cast project.
What is Metal Casting?
Metal casting is a manufacturing process in which molten metal is poured into a mold to create a desired shape. It is one of the oldest and most versatile methods of producing complex metal parts and components. The process involves several steps, from creating the mold to pouring the molten metal and allowing it to solidify.
Casting processes are used to make components out of various materials. For this article, we are going to discuss aluminum and zinc aluminum metal castings. Metal castings are used to create a wide range of parts, from small intricate components to large and complex structural pieces. The choice of casting method depends on factors like the desired part complexity, material type, quantity of parts required, and the quality standards to be met.
1.) Green Sand Casting
Green sand casting, also known as green sand molding, is a popular, economical, and widely-used process for producing simple and complex metal parts, particularly for small to medium-sized casting applications. Due to its consistent, repeatable nature, green sand casting has been utilized as a casting resource for several hundred years.
Green sand casting does not refer to the color of the sand but its use of natural ingredients: a mixture of mined Olivine sand, Bentonite clay, and water. Green sand casting has several advantages, including its low cost, ability to produce complex shapes with good dimensional accuracy, and more. It is used to make various metal parts, including pump housings, medical device bases, handles, enclosures, gearboxes, and other components for industrial and capital equipment manufactured products.
This casting process is excellent for various applications; however, other methods may be preferable for large parts or ones that require a smoother as-cast finish. If needed, corebox(es), part of the tooling, are routinely made to produce castings with internal or external undercuts and/or hollow features.
2.) No-Bake (Air Set) Sand Casting
The No Bake (Air Set) sand casting process utilizes chemical binders to bond the molding sand, which is mixed with a catalyst. As the sand exits the mixer, the binder begins the chemical process of hardening. The sand is pressed against a “positive” pattern shape to create one side of the mold. The same process is used to create the second half of the mold. The top mold is known as the cope and the bottom mold as the drag. The sand molds are removed from the patterns using equipment to manipulate the large molds.
There are several advantages to this type of casting. Like green sand casting, it is relatively inexpensive since it does not require metal dies. The no-bake (air set) process is ideal for creating large, deep, high-value, and heavy castings in a single mold. It allows you to produce components weighing upwards of 50 tons.
The no-bake process is most often used to create large and complex cast geometries. The thinnest wall section (geometry dependent) for a no-bake (air set) sand casting is 0.125” (3mm), most thin-walled components will be made closer to 0.160” (4mm) and larger geometries at 0.200” (5mm) or thicker. This is General Foundry’s largest envelope-size process, creating shapes up to 6 feet (1.8M) in diameter by 4 feet (1.2M) deep and up to 500 pounds (227kg) in weight.
Again, if needed, corebox(es) are made to produce castings with internal or external undercuts and/or hollow features.
3.) Permanent Mold Castings
Permanent mold casting is similar to die casting in that it uses a metal mold or negative die. The molds are designed to withstand repeated use, hence the name “permanent mold.” The process also shares some similarities with sand casting since molten metal is poured into a mold negative which is clamped shut until the material cools and solidifies into the desired part shape. The permanent mold process is the closest process to die casting General Foundry offers and is used to create geometries that require increased structural integrity and intermediate to higher production volumes.
The biggest advantage of permanent mold castings are dimensional repeatability, slightly increased material properties, and a lower casting piece price. This process also creates metal parts with a good surface finish. If the geometry dictates, sand corebox(es) are made to produce castings with internal or external undercuts and/or hollow features.
4.) Rubber Plaster Mold Castings
Rubber Plaster Mold casting (RPM) is a metal casting process that utilizes a flexible rubber tool and a plaster material mold to produce intricate, highly detailed aluminum or zinc aluminum castings. The plaster mold is created from a rubber pattern or master model. A plaster material is poured against the rubber pattern halves to make two plaster mold halves, which are cured and then removed from the pattern. Plaster corebox(es) are made to produce castings with internal or external undercuts and/or hollow features.
This process is often used in applications similar to die castings since the plaster mold will give you the same characteristics (smooth surface finish, thin walls, and complex geometries) as a die-cast part. After the casting is removed from the mold, it is cleaned and finished to produce a final product with a high degree of detail and accuracy. RPM castings are ideal for creating intricate parts with thin walls and complex geometries. The process is excellent for both prototypes and low-volume production.
5.) Investment (Lost Wax) Castings
Investment Casting, also known as Lost Wax Casting, is a manufacturing process used to create metal parts by pouring molten metal into a mold made from a wax pattern. The term “Lost Wax Casting” comes from the fact that the wax pattern is melted away or “lost” during the casting process. The name “Investment Casting” comes from the solid plaster mold or ceramic shell used in the process, called an “investment.”
Investment or Lost Wax Casting is a highly precise and flexible process that allows for the creation of complex parts with tight tolerances and fine details. This process can enable you to combine different wax patterns to create a single mold. This gives you casting options that would otherwise only be achievable through welding cast parts together.
This process also has a tighter tolerance, about 0.003 inches (0.076mm), than other types of casting procedures. Investment casting is one our more expensive production method, which means it is typically reserved for projects where a certain level of precision and composition is absolutely critical. It is commonly used to manufacture parts for the aerospace, medical, and automotive industries, among others.
6.) 3D Printed Sand Mold Castings
3D printed sand mold castings, or additive manufacturing sand casting, is a modern approach to traditional sand casting using 3D printing technology. This method combines the benefits of both additive manufacturing and traditional casting techniques to create intricate and complex metal parts.
3D printed sand molds use layers of sand to create a single-use mold. These molds offer many advantages, including being ideal for creating complex components. Thanks to the use of 3D printing technology, there is essentially no limit to the designs and patterns that can be created. There is also less lead time with 3D printed sand mold casting, it is less labor intensive than other casting processes, and it is also decently cost effective since the “molds” are produced without tooling.
Metal casting is a fundamental manufacturing process that produces complex components used in a wide range of industries. These components form the backbone of various products and systems that are essential to modern life. This article briefly touched on six (6) common metal casting processes. However, selecting the best process for your application can be challenging. A reputable metal caster, such as General Foundry Service, can further advise you on choosing the best process to produce your next high-quality, precision-cast parts.
How can General Foundry Service help you?
General Foundry Service offers true one-stop shopping. With our in-house pattern shop, machine shop, and six complementary casting processes, we offer a best in class turnkey solution for class A coated machined aluminum castings. Contact us today for more information about our clean metal casting solutions or to get started on your next project.